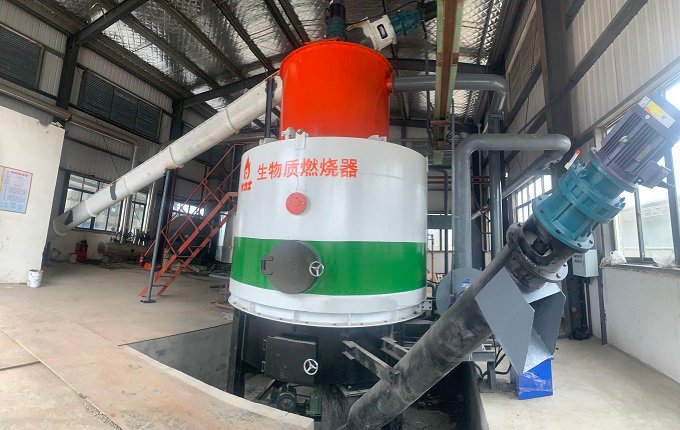
Why you would like it
The biomass-gasificating burner features a rational structure, automatic feeding, and high thermal efficiency.
It adopts semi-gasification combustion, realizing a 99% fuel burn rate, saving energy and materials.
The tangential rotation design ensures complete combustion of smoke and oxygen. And the heat-resistant steel nozzle guarantees zero faults or replacements. Moreover, our special refractory cast materials keep the external temperature below 40°C, which ensures energy efficiency and worker safety.
At last, our star-shaped feeder ensures balanced fuel distribution for precise combustion.
And automatic ash removal, slag discharge and feeding reduce labor intensity, hence a single operator could manage it for 10 hours.
Applicable Fuels
Pelleted Fuel
- Biomass pellets include sawdust pellets, dust pellets, wheat straw pellets, cotton stalk pellets, bagasse pellets, traditional Chinese medicine residue pellets, and rice husk pellets.
Bulk Fuel
- Agriculture and forest waste includes straw, rice straw, rice husks, peanut shells, corn cobs, branches, bark, wet bamboo skins, tobacco stems, coconut shells, bagasse, spent , sawdust, and more.
Applications
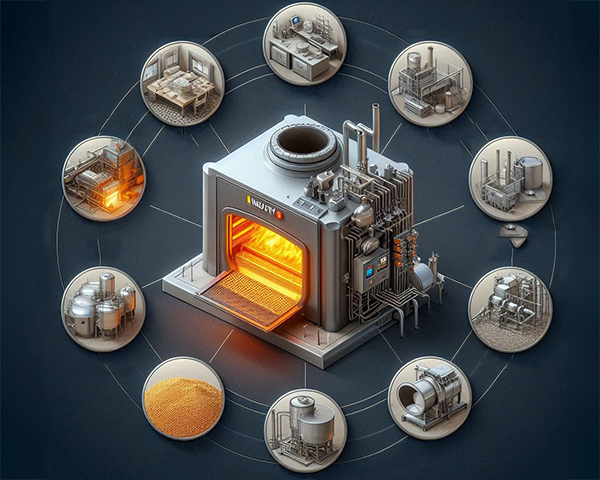
- Hotel loundry
- Grain drying
- Packaging
- Papermaking
- Pharmacy
- Textile
- Garment
- Animal feed
- Winemaking
Features
New generation of biomass fuel saves 30%-60% of operating costs compared to oil, gas, or electric heating boilers. The multiple flue design and secondary oxy-enriched combustion technology, combined with a professional energy saving device make a thermal efficiency of 90%, which is 10% higher than chain boilers.
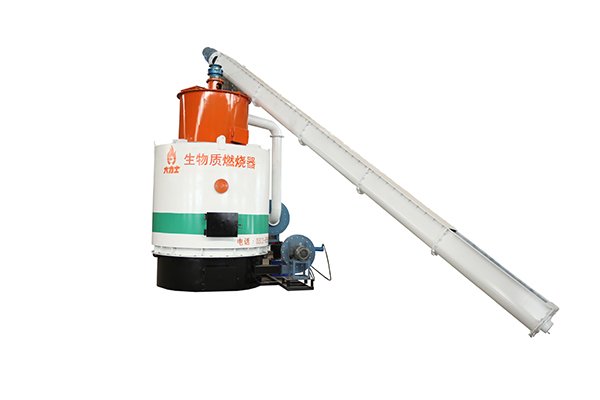
Save more
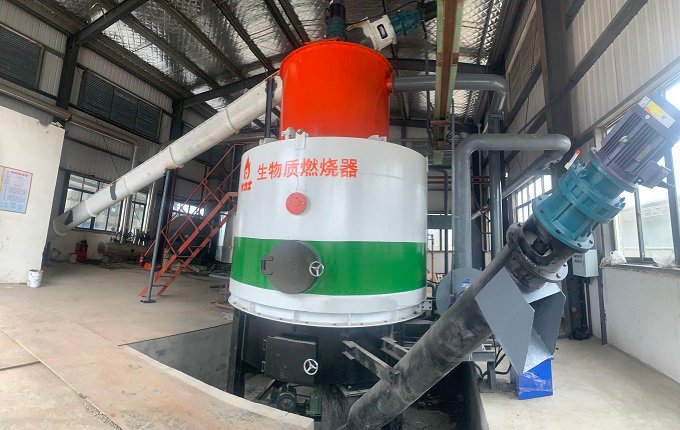
Ultra-low emissions
The biomass burner, through rational design, achieves smoke-free and complete combustion of biomass fuel via semi-gasification technology. Initial NOx emissions are ≤50mg/m³, lower than those in the “Boiler Air Pollutant Emission Standards.” Dust emissions decline by over 90% compared to direct burning.
Multiple interlock protections ensure stable and reliable operation. It also addresses issues of coking and flying ash, making cleaning easy. Automatic constant temperature and pressure, with safe interlock machenism, ensures secure operation.
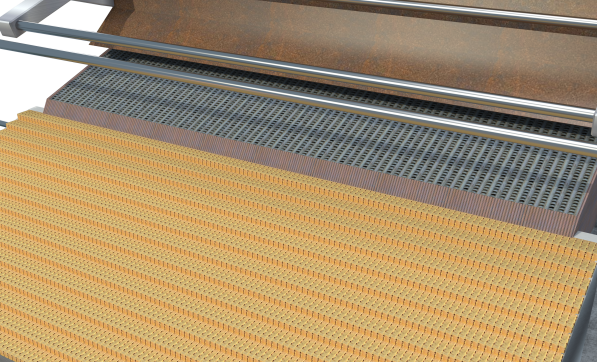
Avoid slag coking
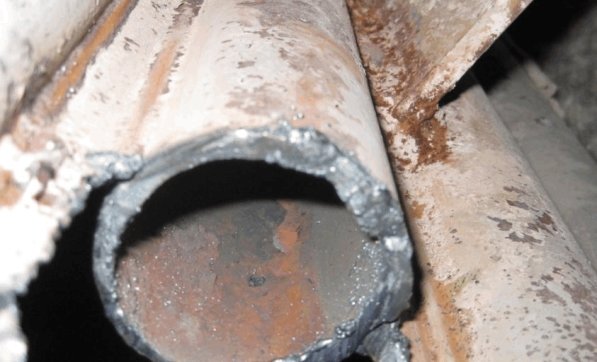
Other tough issues resolved
Effectively solves the problem of alkali metal chloride corrosion. It also uses high-quality nozzles that withstand temperatures up to 1750°C. The patented control cabinet is highly intelligent, stable, and reliable.
Product Design
a. The equipment consists of a gasification chamber and a combustion reduction chamber (secondary combustion chamber). After the fuel is gasified in the gasification chamber, the combustible gases, along with the high-temperature flames, enter the combustion reduction chamber for thorough mixing and combustion, then producing high-temperature output.
b. Tilt Fixed Water-Cooled Grate (TFWG): The gasification chamber uses the TFWG with inclined steel tile outlets. Moreover, the gasification bed is divided into multiple sections with independent air supply. Each section has evenly distributed air plates, with two fans of the same power controlled by a single inverter. This allows precise adjustment of the air supply to each section as needed.
c. Insulated Gasification Chamber: The upper part of the gasification bed is built with an insulated gasification chamber. It maintains a constant temperature, ensuring a stable gasification process.
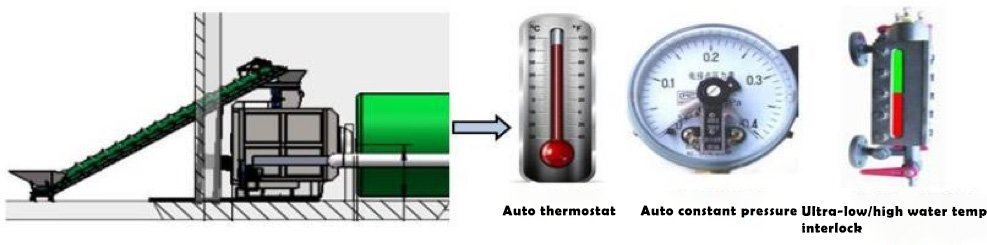
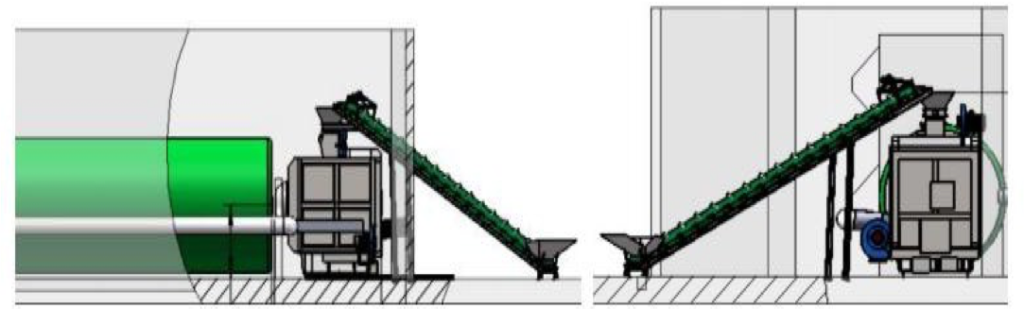
Operating Procedure
01
Fuel feed & Gasification
Fuel is fed through the front hydraulic feeding system. After heating to around 800°C, the feeding system slowly sends the material into the gasification chamber.
Then the fuel undergoes rapid pyrolysis and gasification at high temperatures with partial combustion.
Meanwhile, the high temperature generated from gasification combustion maintains the gasification chamber’s temperature, ensuring continuous high-temperature pyrolysis and gasification.
Thereafter, the remaining unburned combustible gases enter the combustion reduction chamber (secondary combustion chamber) for thorough mixing and combustion.
02
Seconedary combustion
The combustion reduction chamber (secondary combustion chamber) is designed with sufficient space for the combustion reaction.
Meanwhile, firewalls are placed to alter the flue gas flow, increasing the mixure frequency of flying ash with the walls, causing large particles to fall to the bottom of the combustion chamber and be discharged through the ash outlet, reducing flying ash entering the heat exchange system.
Lastly, the extended flue gas path prevents local hot spots, ensuring uniform temperature distribution and significantly reducing NOx formation.
03
Balance of fuel and air supply
The gasifier supplies oxygen from the bottom during the pyrolysis, controlled by a microcomputer.
While the feeding rate and oxygen supply automatically match, optimizing the efficiency of biomass fuel pyrolysis and gasification. Biomass fuel contains 2-4% ash that shall be continuously discharged to maintain heat output.
Moreover, the gasifier works with an automatic ash discharge system that discharges ash based on fuel quality and consumption.
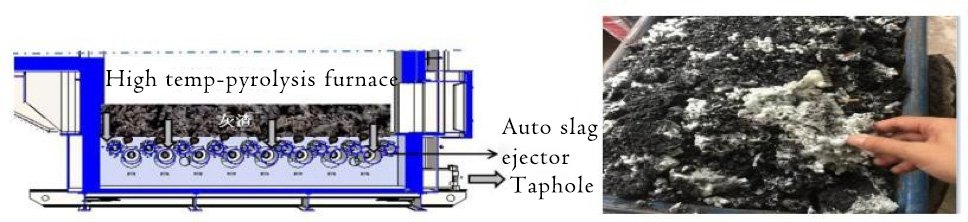
Gasification Technology
- No Change in Burning Method: Compatible with gas/oil boilers without altering the combustion method.
- Wide Applicability: Suitable for retrofitting existing boilers or industrial kilns, replacing high-pollution fuels like coal, heavy oil or wood.
- Low Emissions: CO2 emissions are almost “zero,” with low SO2 and NOx emissions, and dust emissions reduce by over 90% compared to direct combustion.
- High Efficiency and Energy Saving: No need for additional fuels or chemicals. Biomass fuel is directly switched to thermal energy.
- Easy Operation: Fully automatic control with a display screen for monitoring the operation status.
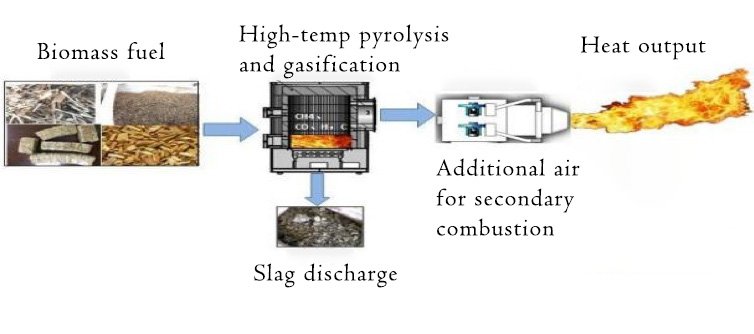
Specifications of Biomass Pellet Burner
Model | Calorific (Mcal.) | Max. Power (Kw) | Fuel Type | Max. WGT. (Metric Ton) | L*W*H (mm) |
2T | 120 | 24 | Multiple | 4 | 2250*1750*3060 |
4T | 240 | 26 | Multiple | 5 | 2520*1970*3185 |
6T | 360 | 29 | Multiple | 7 | 2870*2170*3530 |
8T | 480 | 61 | Multiple | 10 | 3200*2400*5314 |
10T | 600 | 61 | Multiple | 14 | 3700*2800*5854 |
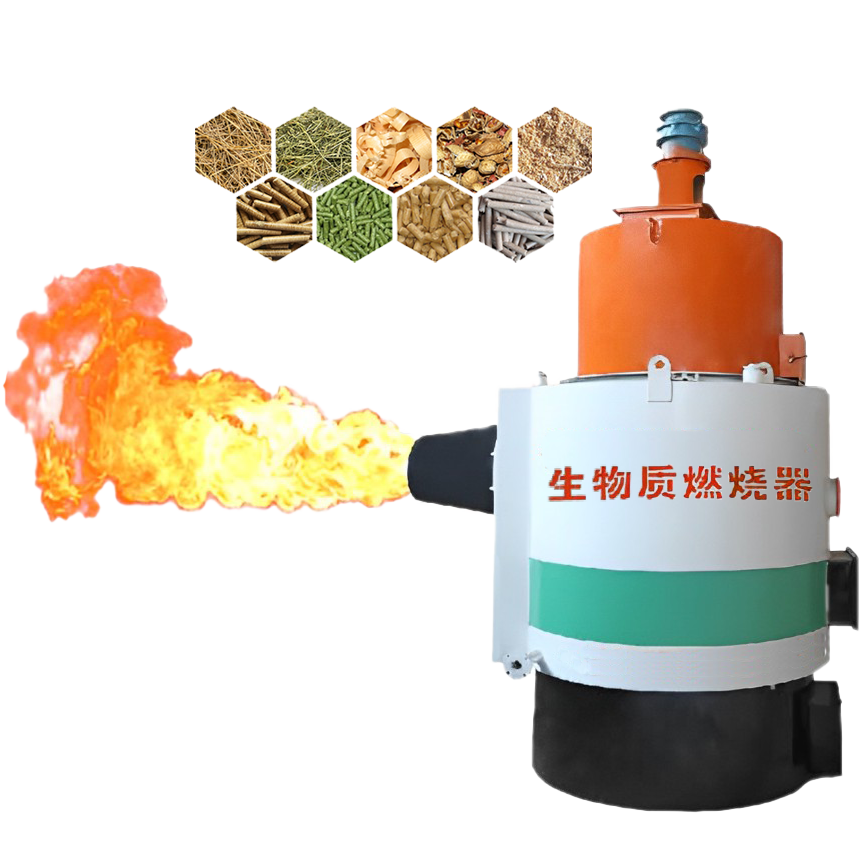
test 7
Pingback: Successful Case - Shengxiang Textile - vgbiomass.com
Pingback: Successful case - Shuntong Organic Chemical Co., Ltd - vgbiomass.com
Pingback: Dust Collector for Biomass Burner
Pingback: How to shut down the biomass burner - vgbiomass.com
Pingback: The Use of a Pellet Burner to Improve Grain Dryer Efficiency - vgbiomass.com
Pingback: Waste Wood Recycling and Biomass Utilization: A Growing Trend in the UK - vgbiomass.com
Pingback: Successful Case – 4T Pellet Burner for 10T Grainer Dryer - vgbiomass.com
Pingback: 4T Biomass Pellet Burner for Food Company - vgbiomass.com
Pingback: Biomass struggles to shoulder important responsibility? - vgbiomass.com
Pingback: Biomass struggles to shoulder important responsibility?(2) - vgbiomass.com
Pingback: Walnut Shells Provide Kinetic Energy for Sodium-ion Batteries - vgbiomass.com
Pingback: IEA: In 2025, Renewables Surpass Coal - vgbiomass.com
Pingback: Expert: Coal-fired units mixed with biomass have significant carbon reduction potential. - vgbiomass.com